제조 과정에서 제품의 품질을 보장하고 안전성을 확보하기 위해 중요한 역할을 하는 비파괴 검사(Non-Destructive Testing, NDT)는 물체의 물리적, 화학적 특성을 평가하고 결함을 감지하는 과정을 의미합니다. 이를 통해 물체의 품질을 평가하고 결함을 사전에 발견하여 사고나 재난을 예방할 수 있습니다. 이번 포스팅에서는 비파괴 검사의 중요성과 원리, 다양한 검사 방법, 그리고 산업 응용 분야에 대해 자세히 알아보겠습니다.
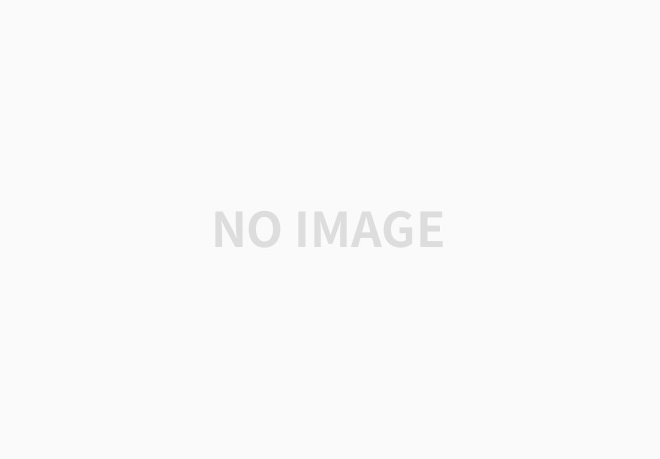
비파괴 검사의 중요성과 목적
비파괴 검사는 물체의 결함을 감지하고 품질을 평가하여 안전성을 보장하는 데에 중요한 역할을 합니다. 그 중요성은 다음과 같은 몇 가지 이유로 설명됩니다.
- 안전 보장: 비파괴 검사를 통해 물체나 구조물의 결함을 정확하게 파악함으로써 사고나 재난을 예방하고 안전성을 보장할 수 있습니다. 항공기 부품이나 철도 구조물과 같이 결함으로 인해 심각한 사고가 발생할 수 있는 경우, 비파괴 검사는 사전에 문제를 파악하여 안전을 확보합니다.
- 품질 향상: 비파괴 검사를 통해 제조 과정에서 발생할 수 있는 결함을 조기에 발견하고 수정함으로써 제품의 품질을 향상시킵니다. 이는 고객 만족도와 제조업체의 신뢰도를 높이는 데에 기여합니다.
- 비용 절감: 제품이나 구조물의 결함은 사후 수리나 교체에 많은 비용을 발생시킬 수 있습니다. 비파괴 검사를 통해 결함을 미리 예방하거나 조기에 감지함으로써 이러한 비용을 줄일 수 있습니다.
- 유지보수 계획: 비파괴 검사는 물체의 상태를 정확히 평가하므로 유지보수 계획을 수립할 때 중요한 정보를 제공합니다. 이를 통해 필요한 유지보수를 시기적으로 수행하고 설비의 수명을 연장할 수 있습니다.
주요 원리와 방법
비파괴 검사는 다양한 물리적 원리와 기술을 기반으로 합니다. 각 검사 방법은 특정한 종류의 결함을 감지하고 품질을 평가하는 데에 최적화되어 있습니다.
1. 초음파 검사 (Ultrasonic Testing, UT)
초음파 검사는 초음파 파동을 이용하여 물체의 내부 구조를 검사하는 방법입니다. 초음파를 발생시켜 물체 내부를 통과한 후 반사되는 파동을 분석하여 결함의 위치와 크기를 확인합니다. 고밀도 물질에서도 효과적으로 사용할 수 있어 금속, 세라믹, 복합재료 등 다양한 재료의 검사에 활용됩니다.
2. X선 검사 (Radiographic Testing, RT)
X선 검사는 X선을 사용하여 물체 내부의 결함이나 불순물을 감지하는 방법입니다. X선을 투과시키고 투과된 선량을 측정하여 결함을 파악합니다. 용융 및 주조 산업에서 금속 부품의 내부 결함을 검사하는 데에 주로 사용됩니다.
3. 자기 입도 검사 (Magnetic Particle Testing, MT)
자기 입도 검사는 자기장을 이용하여 물체의 표면과 근거리까지 결함을 감지하는 방법입니다. 자기화한 물체에 자기 입도 파우더를 뿌려 결함 부위의 자기력을 확인합니다. 금속 물체의 표면 결함 검사에 널리 사용됩니다.
4. 액체 입도 검사 (Liquid Penetrant Testing, PT)
액체 입도 검사는 표면 결함을 감지하는 방법으로, 표면에 액체 입도 소재를 도포한 후 결함이나 균열로부터 물질이 침투되는 것을 확인합니다. 금속, 유리, 세라믹 등 다양한 재료의 표면 결함 검사에 사용됩니다.
5. 산화 환원법 (Eddy Current Testing, ECT)
산화 환원법은 전류와 자기장을 이용하여 물체의 표면과 근거리 결함을 검사하는 방법입니다. 전기적인 방법으로 물체의 전기적 특성을 측정하고 이를 통해 결함을 감지합니다. 금속 및 전기 전자 산업에서 사용됩니다.
주의사항
비파괴 검사를 통한 분석 시에도 다음과 같은 주의사항이 요구됩니다.
- 검사자의 경험과 능력: 비파괴 검사는 정확한 결과를 얻기 위해 검사자의 경험과 전문성이 필요합니다. 검사자는 검사 기술을 잘 이해하고 검사 과정을 정확하게 수행해야 합니다. 부적절한 검사 기술 사용이나 부주의한 검사 과정은 잘못된 결과를 초래할 수 있습니다.
- 검사 환경: 검사 환경은 검사 결과에 영향을 미칠 수 있습니다. 온도, 습도, 먼지 등의 환경 요인은 검사 결과의 정확성을 감소시킬 수 있으므로 이러한 요소를 고려해야 합니다. 특히 액체나 가스가 사용되는 경우 환경 요인에 더욱 민감할 수 있습니다.
- 재료와 두께 제한: 각 검사 방법은 특정한 재료와 두께에 최적화되어 있습니다. 따라서 검사 대상 물체의 재료와 두께를 고려하여 적합한 검사 방법을 선택해야 합니다. 물체의 두께나 재료가 검사 방법의 한계를 초과할 경우 정확한 검사 결과를 얻기 어려울 수 있습니다.
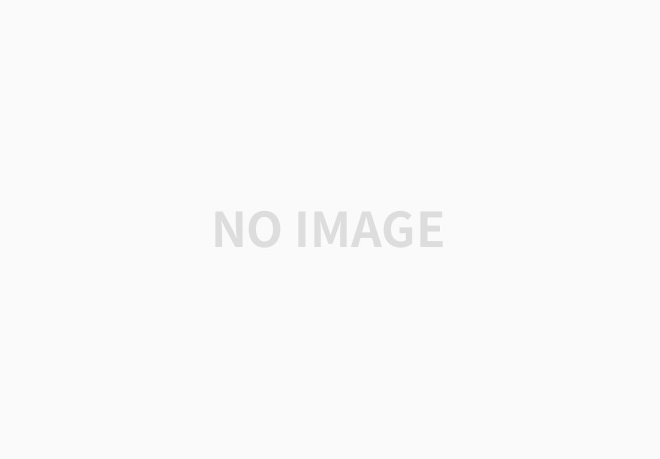
한계
비파괴 검사는 효과적인 품질 관리와 안전 보장을 위한 중요한 도구입니다. 그러나 몇 가지 한계를 알고 있어야 합니다.
- 모든 결함을 검출하지 못할 수 있음: 비파괴 검사는 모든 종류의 결함을 100% 검출하지는 못합니다. 특히 매우 작은 결함이나 표면에 가려진 결함은 검출하기 어려울 수 있습니다. 또한 검사 기술에 따라 특정 종류의 결함을 감지하는 능력이 제한될 수 있습니다.
- 인간 요소의 영향: 검사 과정에서 검사자의 판단과 기술력이 검사 결과에 영향을 미칠 수 있습니다. 검사자의 주관적인 판단이나 실수가 결과의 정확성에 영향을 줄 수 있으므로 검사 과정을 표준화하고 훈련된 검사자를 사용하는 것이 중요합니다.
- 장비 및 설비 한계: 각 검사 방법은 특정한 장비와 설비를 필요로 합니다. 이러한 장비와 설비의 한계로 인해 검사 대상 물체의 크기나 형태에 제한이 생길 수 있습니다. 또한 장비의 정확도와 성능에 따라 검사 결과의 신뢰성이 달라질 수 있습니다.
- 표면 결함 감지 한계: 일부 검사 방법은 주로 물체의 표면 결함을 검출하는 데에 효과적입니다. 내부 결함이나 깊은 위치의 결함은 감지하기 어려울 수 있습니다. 따라서 내부 구조의 검사가 필요한 경우 다른 검사 기술을 고려해야 할 수 있습니다.
추가적인 주의사항과 한계를 고려하여 비파괴 검사를 신중하게 계획하고 수행하는 것이 중요합니다. 이러한 요소들을 고려하면서 검사 방법을 선택하고 검사 과정을 수행함으로써 정확하고 신뢰성 있는 검사 결과를 얻을 수 있습니다.
결론
비파괴 검사는 제조 과정과 제품의 품질 관리에 중요한 역할을 하는 효과적인 방법입니다. 다양한 검사 기술을 활용하여 물체의 결함을 감지하고 품질을 평가함으로써 안전성을 확보하고 비용을 절감할 수 있습니다. 하지만 전문성과 주의사항을 유지하며 검사를 수행하는 것이 필요하며, 끊임없는 기술 발전과 함께 더욱 정확하고 신뢰성 있는 검사를 위한 연구와 노력이 필요합니다.
'공학 이야기' 카테고리의 다른 글
FRACAS (Failure Reporting, Analysis, and Corrective Action System) - 장애 보고, 분석 및 개선 시스템 (0) | 2023.08.22 |
---|---|
Failure mechanism: 시스템 분석과 신뢰성 평가를 결정하는 지표 (0) | 2023.08.21 |
고장분석장비3 폴리싱 - 표면 처리와 단면 분석(Cross section) (0) | 2023.08.21 |
고장분석장비2: Scanning Acoustic Microscopy (SAM) (0) | 2023.08.20 |
고장분석장비 1: SEM-EDX(Scanning Electron Microscope-Energy Dispersive X-ray Spectroscopy) (0) | 2023.08.18 |
VVC(Vacuum Variable Capacitor): RF 응용분야의 고성능 튜닝 솔루션 (0) | 2023.08.18 |
ISO 인증: 품질과 안전을 보장하는 경영 체계의 표준 (0) | 2023.08.17 |
품질 기능 배치(QFD): 제품의 고객 중심 설계와 품질 향상의 핵심 도구 (0) | 2023.08.17 |